
How to Put Tracks Back on a Mini Excavator
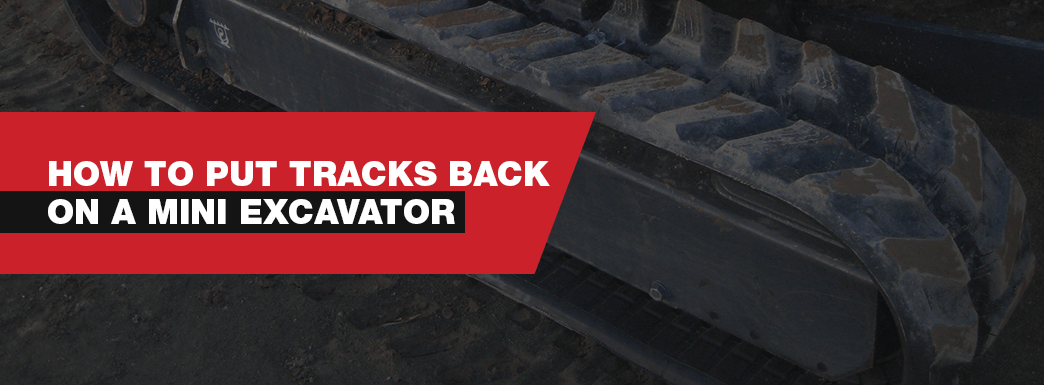
Mini excavators are fantastic tools for a wide variety of jobs. They can maneuver into tight spots and perform plenty of tasks — unless their tracks fall off. When a track comes off of a mini excavator, it can be a frustrating experience, especially if it happens repeatedly. Loose tracks can lead to detracking and premature wear and tear, along with expensive replacements.
Thankfully, you don't need an expert to put the track back on, and keeping the track from loosening in the first place only requires a little maintenance. Learn more about what to do when a track comes off a mini excavator and how to put tracks back on.
How Often do Mini Excavators Lose Tracks?
Mini excavators can lose their tracks more or less often depending on usage. A heavily used machine will lose tension more quickly than one that sees light use. Certain environments can also contribute to tension loss and make an excavator more likely to lose its tracks. Harsh terrain can also affect the tracks' tension and cause it to pop off more frequently.
Following appropriate maintenance and keeping a close eye on your components can help you detect any losses in tension and help you prevent losing tracks.
Signs Your Tracks May Be Coming Loose
So how do you tell if your tracks are getting loose? Fortunately, mini excavators provide you with quite a few signs to alert you of this condition. Below are some of the telltale signs that your mini excavator tracks are getting loose.
1. Sprocket Issues
The sprockets take care of the rotation of the track. They typically interlock with and move it around, but if they start to skip over lugs, you may have an issue. If they aren't interlocking appropriately, the track can come off. The skipping is a sign that your track may be loose or your sprocket is worn. Keep an eye on the condition of the sprockets.
2. Lost Tension
As you may expect from something made of rubber, tracks stretch with use. Check the tension regularly, depending on how often you use the excavator. If you use it heavily, check it every few days.
To check the tension, lift the tracks off the ground by moving the boom to one side and pushing it onto the ground. Then, examine the distance between the middle roller and the track. Check manufacturer specifications for a specific length to look for. An inch between roller and track tends to be average. If the distance is too wide, the wheels need tightening. Paying attention to track tension can help you extend the excavator's life and keep components in good condition.
3. Missing Lugs
Missing lugs can spell trouble for your track tension. The lugs may come out from sprockets slipping against them or if they are damaged. Look at the condition of the parts regularly to make sure they aren't affecting the tension of your tracks. Replace any missing lugs right away.
4. Cracking
Usage will affect the rubber on the outside of the tracks. Certain environments, like rocky terrain, can more quickly cause cracks to appear, and so can heat or sun exposure. Once cracks show up, you should replace your tracks. High-quality rubber can better resist cracking, and storing your mini excavator out of direct sunlight can help.
5. Deterioration
Deterioration can similarly cause premature wear on your tracks. If they are exposed to excessive heat, damage or sunlight, you may find stress marks or even rotting rubber. If your tracks begin to deteriorate like this, it's time for a replacement.
Fortunately, many of these problems are preventable with regular maintenance of your compact excavator. We'll get into track maintenance tasks later, but first, let's take a look at what happens if your tracks do manage to come off of your mini excavator.
How to Put Tracks Back on Your Mini Excavator
Putting the tracks back on a mini excavator doesn't require any advanced knowledge, just a little elbow grease — and some real grease, of course. Thankfully, it's a relatively quick process, though you'll probably need a friend to help you out.
You will need:
- A socket set
- Grease
- A grease gun
- Pry bars
Here's how to fix your tracks:
- Setup: Raise the side of the track you are trying to fix by pushing the boom into the ground on the side you're working on. If your excavator is in an uneven location, you can use the boom to help you "walk" it to level ground.
- Remove grease: Open the panel above the tracks that contains the grease fitting or zerk. Use a wrench to remove the top fitting. Grease should start to flow out, releasing tension in the tracks. Clear out the grease. The track should be almost completely slack.
- Move track: Use your pry bar to pull the track over the wheel. Rotate the track so it locks onto the wheel. Here's where you may need a second person to help you out, as the tracks are heavy.
- Regrease: Hook up your grease gun to the fitting and pump grease back in to increase the tension until the tracks are appropriately tightened according to manufacturer specifications.
- Attach panel: Reattach the panel and you're ready to get back to work.
That's all it takes to get your track reattached to the mini excavator so you can keep moving. If you think your machine might be configured in a unique way, it may help to check the owner's manual for more information on where certain components are, such as the grease fitting.
How to Prevent Tracks From Coming Off a Mini Excavator
The reasons that tracks can come off of a mini excavator are numerous, but not too difficult to address. With proper maintenance and a watchful eye, you can keep your tracks in place. Below are some of the reasons your tracks may come off and what you can do to prevent it from happening again.
1. Check Your Tension
Tension is a common cause of loose tracks. Tension can change throughout the life of your tracks, and different applications require different tensions. The manufacturer should provide you with a recommended tension level, often in the form of the distance between the roller and the tracks. While knowing the recommended tension can help you maintain a general tension level and ensure it doesn't become too loose, specific driving conditions may warrant special attention. Soft ground might require tracks with more slack, while hard or rocky ground may need slightly tighter tracks.
Loose and tight tracks are both problematic, so you'll need to get them just right to avoid difficulties. When tracks are too loose, you risk the track coming off during operation, particularly while taking turns or traversing an uneven surface. Detracking can be dangerous to anyone in the vicinity, plus the tracks are difficult to reattach. Tracks that are too tight, on the other hand, increase wear and tear on your excavator. Components will see unnecessary strain and may not last as long as they should.
Another significant component of getting the right tension is knowing the difference between the needs of steel and rubber. Rubber tracks typically need to be tighter, while steel tracks can be looser. Steel doesn't flex and needs a way to relieve the buildup of tension from any material that gets stuck in the tracks. Rubber tracks are more flexible, so they tend to adjust to these objects on their own and don't lose as much tension when they appear. Tightness should be adjusted if switching between steel and rubber tracks. Always check the manufacturer's specifications to know what this should look like.
2. Keep Components and Undercarriage Clean
Mini excavators sometimes get put through the wringer thanks to use in harsh environments. They might be found in terrain that is rocky, muddy, sandy, soft or filled with rubble. Keeping them clean and in good condition can be difficult but it is a vital step toward extending the life of your equipment.
Rollers need to move smoothly and flanges should not be dull and rounded. Worn sprockets are a common problem area and can affect track stability. Of course, inspecting these elements requires them to be cleaned. Removing a layer of mud lets you see any signs of wear and tear. Wash your machine after each use and thoroughly inspect it, looking for any worn parts. Any dirt and debris that stick in the undercarriage can cause your tracks to wear from the inside.
Materials like debris, mud, gravel and rubble that get stuck in the tracks can become compacted over time. Compacted material increases the tension on the tracks. To clear it, get in the habit of raising the tracks and running them quickly to clear out the debris. You can also lower tension by releasing grease.
3. Make Sure the Adjuster Piston is Working
When you put grease into the machine, what you're really doing is pushing an adjusting piston in a way that increases pressure on the tracks. The mechanism is what tightens the tracks. If the piston is rusted, bent or otherwise deteriorating, it can loosen over time and cause tension to fall away, loosening your tracks to an unacceptable level. A faulty adjuster piston may be what causes the tracks to fall off.
To see if this is the case, tighten your tracks in the morning and check the tension throughout the day. If it falls quickly, the piston could very well be your problem.
4. Follow Best Practices for Operation
While we all like to think we're great drivers, rough operation can exacerbate many problems from loose tracks. Remember to follow safety guidelines and drive carefully.
- Steer to avoid driving over objects or
- Drive straight up slopes, rather than sideways.
- Use a wider radius when turning to keep both tracks on the ground.
- Drive at the recommended speed or even slower.
- Go forward, rather than in reverse.
- Limit traveling over curbs and sharp edges.
- Protect your mini excavator from direct sunlight.
- Keep up with maintenance and cleaning.
5. Purchase the Right Tracks
It's important to buy tracks that fit your equipment. Tracks that are ill-fitting or poorly made will see a host of problems, including reduced tension. Some signs that your track doesn't fit correctly include:
- Too much space between components: If the track bangs against the sprocket during operation, it probably doesn't have a tight fit.
- Incorrect seating: If the seating slips or the tracks don't stay on, it may not be a match.
- Track rollers push on material: Tracks that take on divots or grooves from the rollers are a sign of a track that is too small or incorrectly sized.
To find the right size, compare the new tracks with your previous ones, check with the manufacturer or give us a call. Our staff is full of professionals who deal with track sizing every day and can help you find the right ones.
Poor construction practices or low-quality materials can also affect your tracks' performance. Too much flexibility is a common problem with poor-quality tracks. If the cables within the tires are weak or the material is too thin, the tracks could easily lose their rigidity. Durable tracks are a necessity for the environmenthow s that many mini excavators are in. High-quality rubber can better stand up to sun damage or high heat exposure, too. Depending on your work environment, this may be an important factor in your workday and could lead to early wear if not addressed.
Don't forget about matching your tracks to the industry you're in. Demolition and construction sites need durable tracks, possibly steel, while landscapers might need gentler, smooth tracks that won't damage the ground. Other industries have unique needs, and fitting your tracks to the job can offer a variety of benefits.
Find the Right Tracks with McLaren
When it comes to buying high-quality, well-fitted tracks, the professionals at McLaren Industries are ready to help. We know tracks and can help you find the right ones for your machine, industry and needs. We have tracks for mini excavators from major brands like CAT®, John Deere, Kubota and more.
In addition to tracks that are well-made, our pattern designs provide exceptional performance in various conditions, like snow, mud and rocky ground. Our NextGen premium-quality track series, designed to optimize the life of undercarriage components, helped solidify McLaren as a leading rubber track manufacturer worldwide. We've even come up with a HYBRID series of steel and rubber tracks that are virtually indestructible. All of these products are available for mini excavators and are backed by the expertise and support of McLaren Industries, where we've been keeping machinery moving for over 25 years.
Request a quote or give us a call today at (800) 836-0040 for help choosing the right mini excavator tracks for your next job.